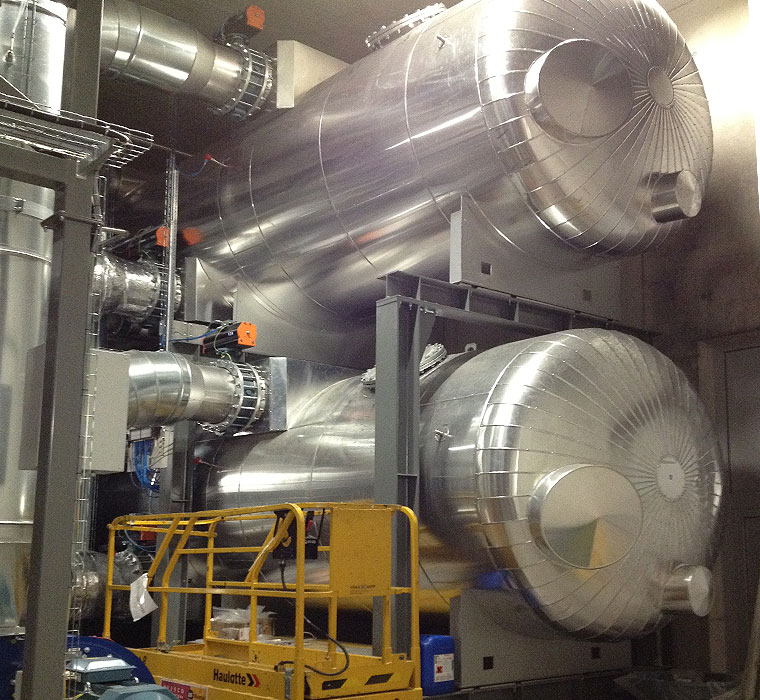
This plant is ideal for companies producing EPS and expanded polyurethane, offering not only the possibility to comply with emission regulations, but also to recover and sell the solvent, turning an obligation into a profit opportunity, all with a reduced investment.
Pentane is a hydrocarbon widely used in the polystyrene expansion process. During this process, polystyrene beads are impregnated with pentane and exposed to a flow of steam, which causes the pentane to evaporate and the beads to expand up to 20 times their volume. Of the pentane used in the process, one third remains in the beads, while the remaining two thirds are released into the atmosphere, polluting the surrounding air.
The advantage of the ULIX INNOVATION process is that it purifies the air by recovering pentane and reusing it in a closed-loop process. The benefits are not only environmental but also energetic (pentane can be used as boiler fuel) and economic (through the sale or reuse of pentane as a raw material). The ULIX plant captures all pentane-contaminated air flows coming from various emission points (pre-expander, silos, block molding machine) through a branched suction system that automatically adjusts to the air flow required by the process, depending on the phase of production.
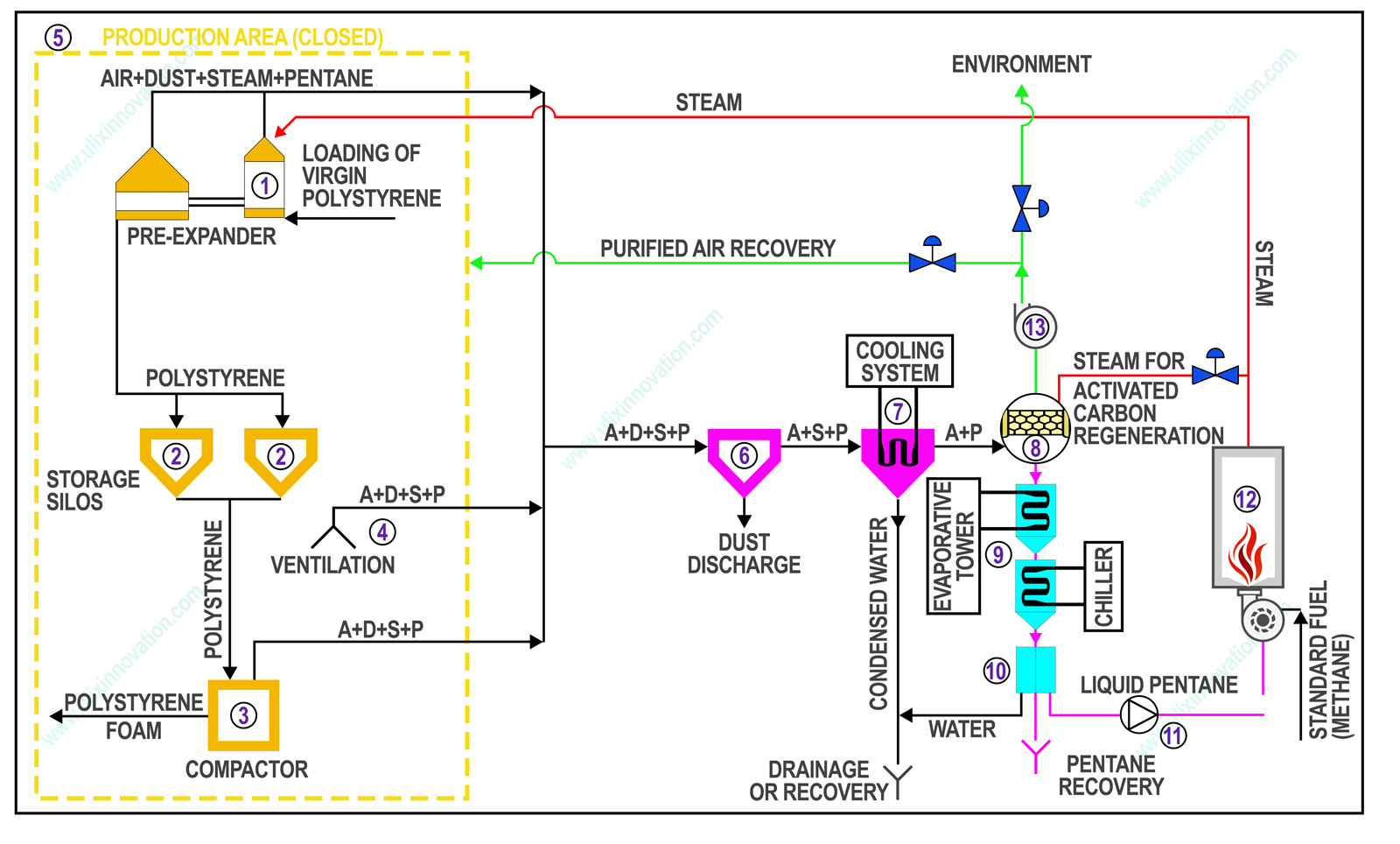
The contaminated air, loaded with water vapor, after dust removal and vapor condensation, is sent to one or more activated carbon adsorbers, where the pentane is trapped. The solvent is then recovered through a steam flow, which simultaneously regenerates the activated carbon. It is then condensed by the combined action of an evaporative tower and a chiller, decanted, and separated from the water in liquid form.
The recovered pentane is stored in a dedicated tank and can be reused in the production process of expanded polyurethane or expandable polystyrene. Alternatively, it can be sent to the boiler burner, which produces steam for the expanded polystyrene production machines. A special burner, provided by us, operates with methane, pentane, or a mix of both. The steam produced by combustion is reused for the polystyrene production processes, as is the air exiting the activated carbon, which is of extremely high purity.
This process allows the plant to operate with ZERO EMISSIONS into the atmosphere, both in terms of pentane and air flow.
The plant is delivered turnkey, complete with control panel, electrical system, PLC, and HMI, installed, calibrated, and ready for production.
ADVANTAGES OF ULIX INNOVATION TECHNOLOGY:
• Very high solvent reduction efficiency (96 ÷ 99.5%)
• Fully GREEN plant (ZERO EMISSIONS)
• Recovery and reuse of recovered pentane = cost savings + minimal environmental impact in the production process
• Government economic incentives in many European and non-European countries
• Low energy consumption and reduced operating costs •Modular system, allowing future expansions based on the treatment capacity required
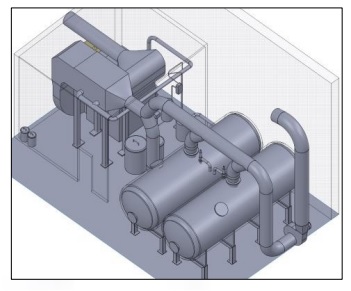
Services offered by ULIX INNOVATION:
• 2D and 3D plant design
• Space study and custom layout realization
• Construction, pre-assembly, and testing in our own workshop
• On-site installation, start-up, and plant calibration
• Collection and purchase of recovered pentane at the client’s site
• Training sessions for personnel on proper plant use
• Remote assistance and plant monitoring