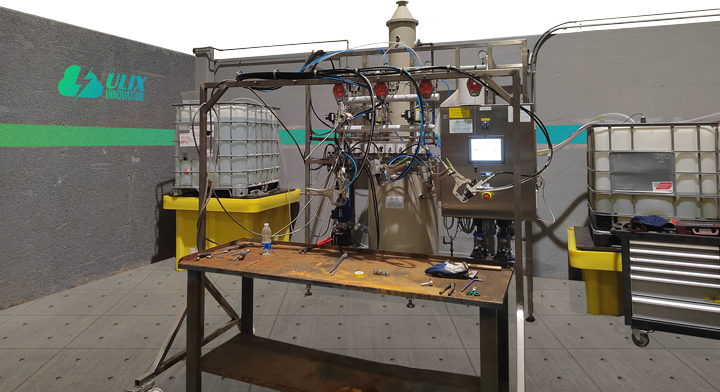
This system is designed for companies dealing with WEEE waste, such as refrigerators, heat pumps, and chillers, ensuring efficient recovery of the refrigerant gases contained in these devices. With the solution offered by ULIX Innovation, you can comply with environmental regulations, reduce disposal costs, and turn a necessary process into an opportunity for savings and profit.
In 2023, Europe saw the generation of approximately 13.5 million tons of Waste Electrical and Electronic Equipment (WEEE), continuing a trend of growth in e-waste production due to increased consumption of electronic devices. These devices contain hazardous substances which, if released, contaminate the environment and require special disposal. Included in this category are the refrigerant gases used in refrigerators and air conditioners: CFCs, also known as FREON. These compounds have a Global Warming Potential (GWP) of 1430 and are major contributors to the depletion of the ozone layer.
The ULIX Innovation system is capable of extracting freon and oil from used refrigerators, recovering the gas with an efficiency close to 100% and a purity exceeding 99%, making it reusable for new appliances.
The process works as follows:
The operator, using a custom-made clamp, punctures the copper tube containing the gas. Once the control system gives all the necessary approvals, the vacuum pump is activated to extract oil and freon. The freon is separated from the oil in a de-oiler: the oil is collected in a storage tank, while the freon continues its process. After being compressed through a compressor and cooled below its liquefaction point, it is stored in a tank and then transferred to a dedicated cylinder.
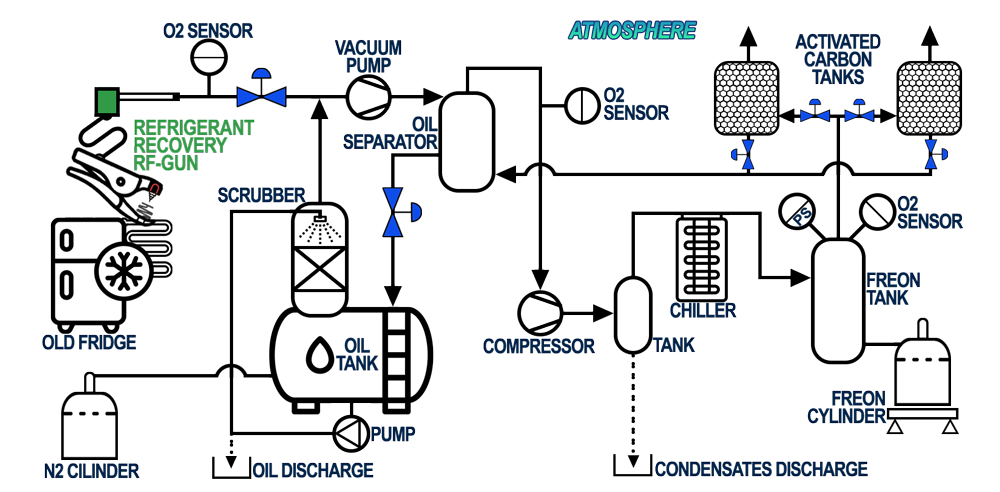
The oil is further purified by stripping the gas dissolved in it, which is then recovered. If there is air in the circuit, a pressure switch will trigger the venting of the gas tank: the air will pass through an activated carbon filter and be released into the atmosphere, while the freon contained in it will also be recovered through the regeneration of the activated carbon.
Due to their high environmental impact, freons have been progressively replaced by R600 and A2L refrigerants. In the case of these compounds, especially R600, the system includes additional safety measures due to the flammability risk, making it compliant with ATEX regulations.
Thus, a sensor will monitor the oxygen concentration in the three most critical points of the system, and before the valve to the gas suction manifold is opened, additional approvals must be verified. If the system detects an oxygen concentration higher than the LOC (Limiting Oxygen Concentration), a nitrogen purge will be activated, blowing out the oxygen from the pipelines.
The system is fully automatic and managed by a PLC, with remote control capabilities and the possibility of being interconnected with the factory’s IT systems.
ADVANTAGES OF ULIX INNOVATION TECHNOLOGY:
• High recovery efficiency (<1ppm)
• ZERO disposal costs
• Low maintenance and mobile flexibility
• Compact and easily movable system
TECHNICAL FEATURES OF THE SYSTEM:
• Study and optimization of the existing production process
• Training sessions for staff to fully utilize the system
• Start-up and monitoring of the system at the customer’s site
• Remote assistance to ensure proper system operation
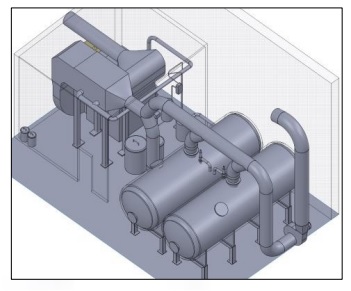
Services offered by ULIX INNOVATION:
• 2D and 3D system design
• Space study and custom layout development
• Testing, assembly, and preparation of the system at our workshop
• Issuance of all certificates and system calibration
• Transport and installation of the system at the customer’s site
• Installation service to ensure proper system functionality
• Preventive maintenance to ensure the correct use of the system
• Technical solutions to minimize downtime