Isododecane is widely used in the cosmetic industry as a solvent for its emollient properties and because it evaporates quickly without leaving residues in the product. For these features it is used to prepare the mixtures that, once dried, generate the end product (face powders, eye shadows, etc…)
Our company has developed a system which completely purifies the processed air,
contaminated by isododecane, in order to regulate the emissions in accordance with the European Directive of 2014 (VOC Solvent Emission Directives) and respective national regulations. The isododecane is recovered in liquid form and will be reused in the production process with the same purity as the virgin product. The emitted stack air can be recirculated in the de siccator, by employing a close loop which brings considerable benefits in economic terms (saving on solvent purchase) and in environmental impact (in full compliance with regulations).
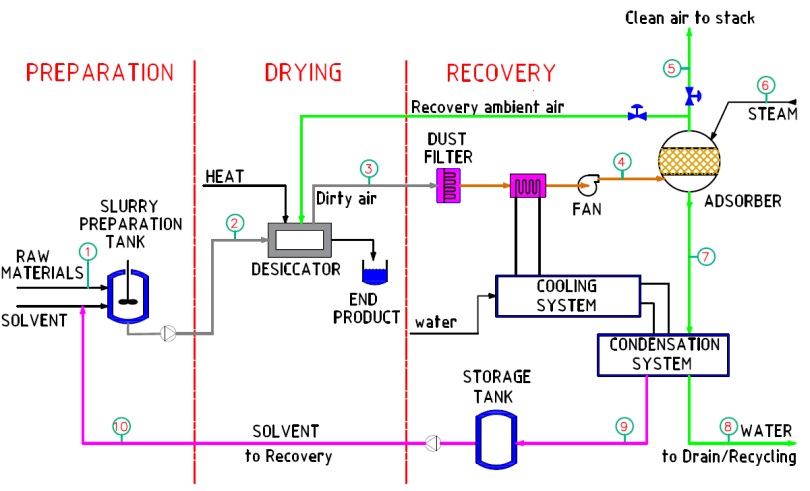
The preparation of the mixture takes place inside special mixing tanks [1]; then the mixture is loaded into the desiccator [2] where heat produces the evaporation of the solvent. The finished product is collected outside the desiccator while the polluted air containing isododecane is sucked-in through a dedicated fan; this is then filtered by any powders, cooled, and sent [4] to the adsorbers (one or more ), where the ACTIVATED CARBON beds retain the isododecane, while clean air is expelled from the stack [5].
Once saturated, the activated carbon is re generated by a water vapor stream [6] to the
adsorber; the steam strips isododecane from carbon and drags it away, restoring the adsorbing capacity of the beds.
Through a system of vapor condensation and separa tion [7], isododecane is recovered with a purity greater than 99% [9] and so it can be reused as raw material in the process [10].
The plant is turn-key supplied with electrical panel, electric system, PLC and operator interface terminal, assembled, calibrated and ready for production. Based on the customer’s needs, we can provide the entire system (preparation + drying + recovery) or the recovery part only. We provide maintenance services in order to guarantee no stop in production.
ADVANTAGES OF ULIX INNOVATION TECHNOLOGY :
– Very high efficiency of the solvent removal (96 ÷ 99.5%)
– 100% GREEN (Zero Emissions)
– Solvent Recovery with its reuse in the production process = economic saving +
zero environmental impact in the manufacturing process
– Low power consumption and reduced system management costs
– Modular plant design which allows successive enlargements according to the flow to be treated
– Return of investment within 3 years (only considering the solvent
recovery)
Technical features “DRYING” section:
– Type of solents to be evaporated Isododecane (or similar solvents)
– Operating temperature 80÷100°C
– Reference standard Directive 2004/42/CE of the European Commission
– Electricity consumption negligible
– Steam consumption about 20÷25 kg/h
Technical features of “RECOVERY” section:
– Air flowrate to be treated from 1.000 to 50.000 Nm3/h
– Type of solvent to be removed isododecane (or other similar solvents)
– Electricity consumption ≈ 10 kW (for every 10.000 Nm3/h of treated air)
– Industrial Water consumption ≈ 0,2 m3/h (for every 10.000 Nm3/h of treated air)
– Steam consumption ≈ 100 kg/h (for every 10.000 Nm3/h of treated air)
Services offered by ULIX INNOVATION :
– Training sessions for staff for the proper use of the system
– Remote assistance and remote monitoring system
– Continuous monitoring of stack emissions
– Study and optimization of existing suction lines
– Maintenance service in situ and warranty of no production stop for long times